Warehouse Fit Outs: 6 Challenges You May Encounter in 2021 and Beyond
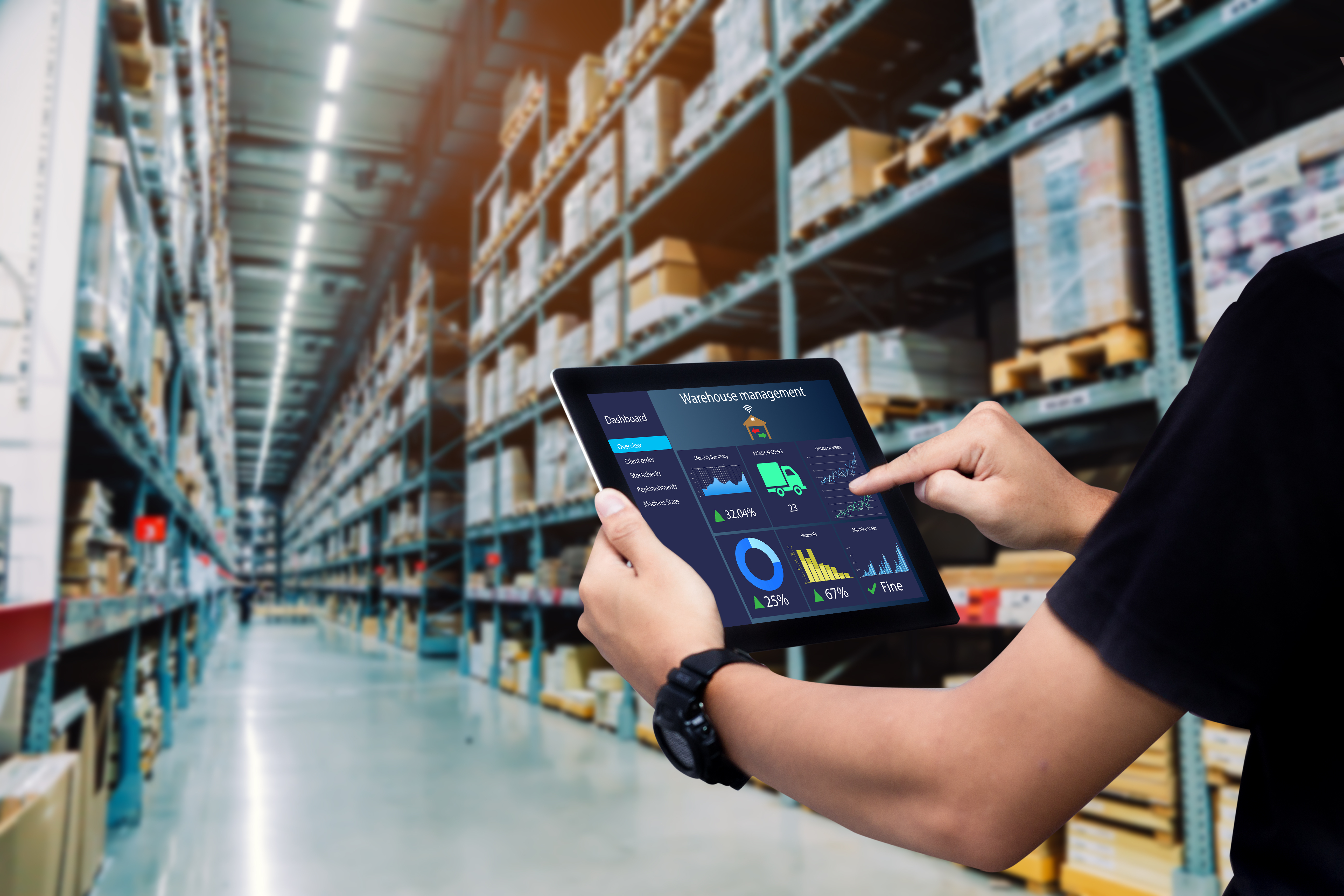
Warehouses can be one of the more difficult spaces to fit out, as they’re not as straightforward as an office or home. As a result, you’ll find that there are a few challenges you may encounter while trying to ensure that the space is functional and maximises performance, productivity and efficiency. In this article, we explore a few of the more common dilemmas that pop up with warehouse fit outs – especially during a pandemic – as well as the solutions that can help you avoid these pitfalls.
1. Inventory inaccuracy
Problem:
Warehouses need to be accurate and efficient when handling inventory – and it is vital now more than ever for businesses to get it right. The COVID-19 pandemic has been wildly unpredictable, even now, more than a year later.
Consumers are panic-buying and stocking up on products in a way that relies on warehouses to maintain a constant supply of inventory. Therefore, it is important to ensure accurate inventory or you could end up with a host of problems, such as maintaining improper stock levels and build-ups of obsolete inventory. In turn, these issues can lead to picking problems, as pickers will now be reliant on inaccurate information, which further leads to inefficient processes.
And these are not the only hurdles you’ll face, as inventory inaccuracy will lead to a domino effect that will result in lower productivity, increased expenses and loss of revenue.
Solution:
Digital tools and technology are being implemented into every type of workspace, from offices to restaurants and retail stores, as it improves productivity and efficiency. By implementing an automated system into your warehouse processes, you can obtain real-time, accurate information on stock levels and composition.
2. Redundant processes
Problem:
Traditional systems see a product being handled by several employees, going hand-to-hand in a seemingly endless cycle before it finally gets to its destination. Two notable discoveries found during the pandemic is that this process posed a health risk for employees and customers, as a product is passed through multiple hands before reaching its final stop, and this system was made up of redundant procedures.
While necessary in some instances, for the most part, these redundant procedures were time-consuming, inefficient and increased the cost of labour
Solution:
This issue is easily solved by, once again, implementing the right digital tools and technology into your procedures. For instance, barcode technology can streamline your warehouse processes by removing redundant functions and maximising resource utilisation.
3. Poor warehouse layout
Problem:
Efficient use of space is a critical success factor for any fit out project. Warehouses, in particular, need an effective layout as they need to house many different areas in one space.
Warehouses with a poor facility layout commonly experience inadequate storage space, as well as an inefficient use of available space. This negative impact stretches even further to decreased levels of productivity and performance, and lower profits.
Solution:
Any interior designer or contractor worth their salt will help you develop and execute an effective layout design for your warehouse space. We strongly advise hiring a reliable and trustworthy professional who comes highly recommended to aid you in your fit out project for the best outcomes.
That being said, optimal warehouse layouts will consider both the floor space and the vertical space for use. Furthermore, a good layout maximises the use of equipment and labour, accessibility to all items, security of all stock, and the safety of employees.
4. Cost of labour
Problem:
The best-run warehouses can increase productivity while minimising labour costs in a labour-intensive environment. Admittedly, this does sound like an impossible task considering that these costs can constitute nearly 65% of the operating budgets of most warehouses.
Furthermore, warehouses typically use expensive equipment, like forklifts, and employ large labour forces that include cleaners, packers, managers, administrative personnel and more. This can prove to be a problem as a business’s main goal is to make a good profit, which is nearly impossible when more than half of your budget is dedicated solely to labour costs.
Solution:
Fortunately, we are living in 2021, where digital tools and technology are revolutionising business processes everywhere. Therefore, the two best solutions on offer for this problem is to maximise available labour and replace labour with automated systems wherever possible.
5. Optimisation of picking strategy
Problem:
You may not even realise this, but your picking strategy could be holding you back. If you’re one of the many warehouse owners or managers struggling to improve operational efficiency, you might want to turn your attention to your picking process.
Believe it or not, picking is where a majority of warehouse management problems occur. This is because poor picking can easily disrupt an inventory control system when the tasks and decisions engaged in daily are done in a hurry to assist an urgent customer in a tense environment.
Solution:
Improving your picking process could go a long way in boosting both employee productivity and your bottom line. But how can you achieve this?
If you rely on a paper-based system, consider switching to radio frequency and voice-directed systems instead. However, regardless of which type is used in your warehouse, the important part is to ensure full compliance with whichever system is implemented – even when circumstances arise that make compliance seem counter-intuitive.
A good way to keep your system accurate and reliable is to integrate logistics technology systems and pay dedicated attention to the master data. And when exceptions do occur in the picking system, such as an approved substitute item or finding an item in the wrong slot, these exceptions need to be recorded to allow for a full and accurate record of inventory.
6. Quality control
Problem:
In most warehouses, workers who are in charge of quality control also find themselves doing the picking, packing and shipping of inventory products. As a result, many errors never get found or picked up until the customer receives the item. This issue is especially prevalent in the current pandemic environment, where warehouses are trying to ship more products with less staff available.
Solution:
The most obvious solution is to separate quality control from the manual processes of picking, packing and shipping. This separate level of authority can provide the motivation to manage everyday inventory issues in a structured manner that encourages accountability.
And, as always, we return to technology being the most effective solution to warehousing issues. A quality control function can record vendor accuracy, improve stock rotation and reduce the need for manual processing of warehouse items.
Need help with your warehouse fit out?
The pandemic has shown us that traditional warehouse processes just aren’t cutting it anymore. It’s time for an upgrade to your workplace fit out.
By introducing a holistic system into your processes will ensure your warehouse has the required flexibility to navigate any storm that comes your way. The more update your WMS technology and the more transparent and accessible your data is, the better your chance of overcoming the above-mentioned challenges.
However, you’re going to need the help of an expert to execute your fit out project successfully. Fortunately, we just know where to find one.
Contractors.Direct offers a curated database of thoroughly vetted, quality contractors, interior designers and interior architects who can bring your vision to life, on time and on budget. Get in touch with us and we’ll be happy to connect you with the right people for the job.
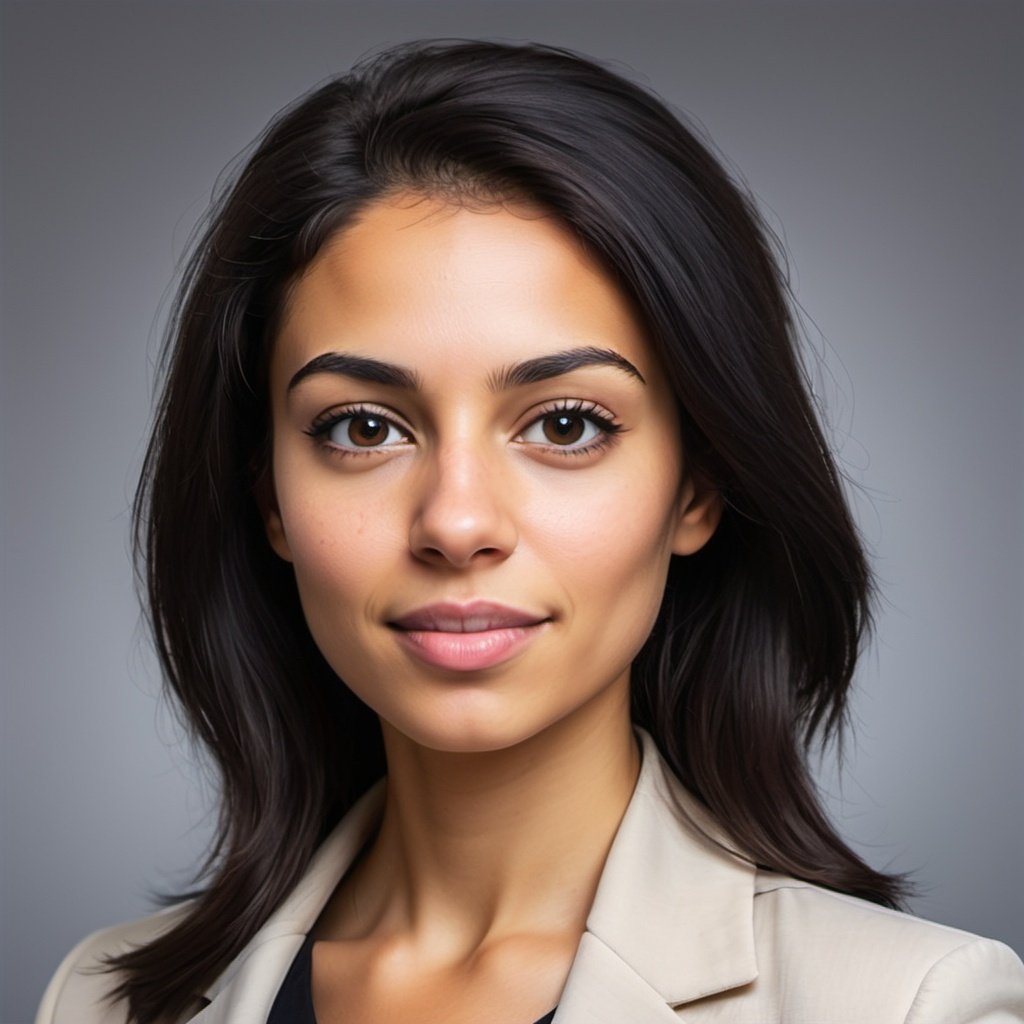
Written by Kirsten Delcie
As a seasoned project professional, Kirsten has been curating and creating content for Contractors Direct since the company's inception. Her diligent research methods and style lend themselves to the valuable insight driven blog posts you see here. Outside of content creation Kirsten is an avid reader and scuba diver and combines both as often as possible!
Ready for a Stunning New Space?
Dream for a new look for your space? Make an appointment today for the perfect contractor for you. We'll work with you to make your vision a reality.
Related Posts
Should Employees Exercise at Work? – 8 Reasons to Build an Office Gym
There has never been a more critical time for employers to prioritise the...
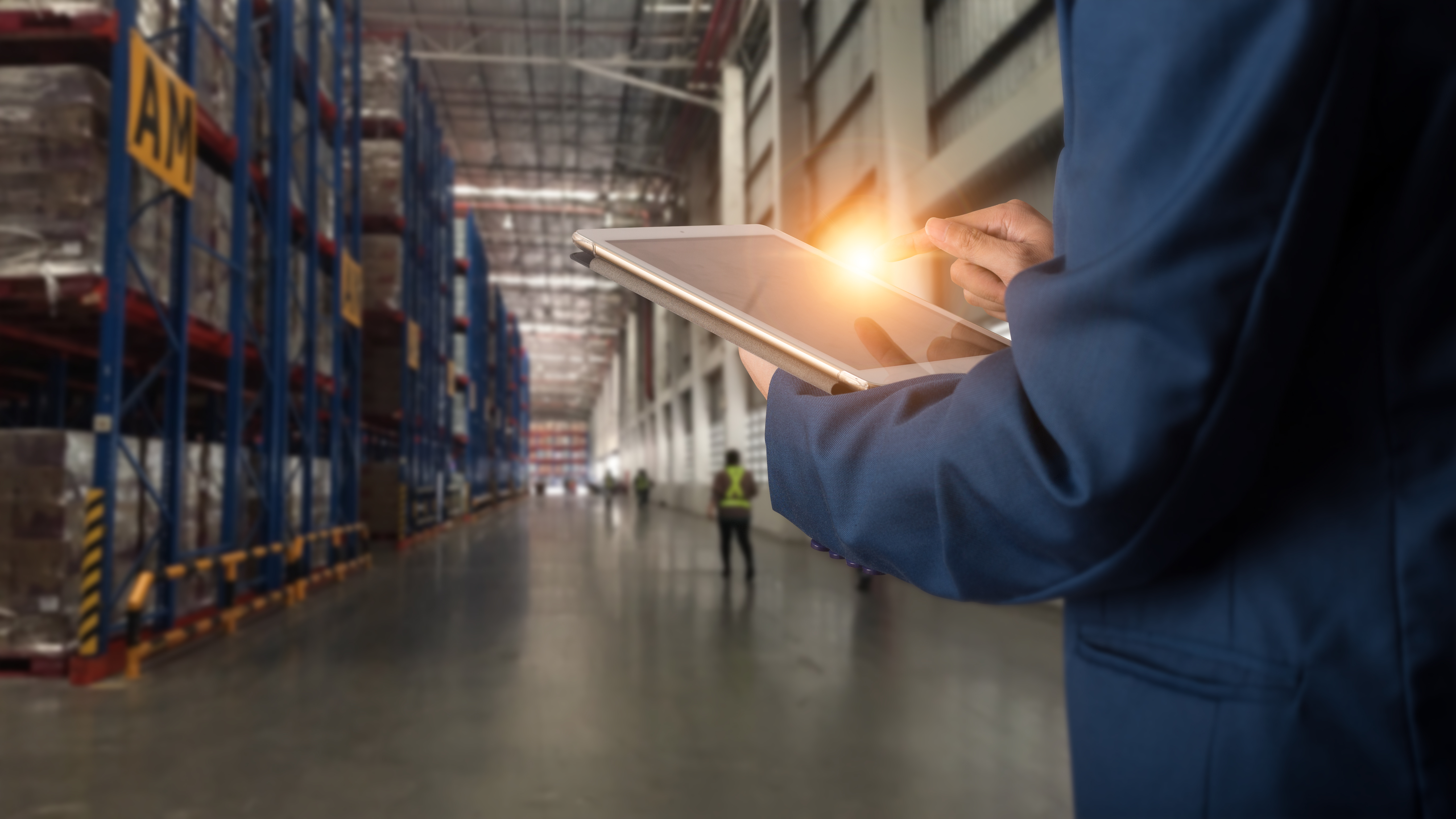
5 Tips to Plan Your Warehouse in 2020
The layout and design of your warehouse have a direct impact on the efficiency...